Welding 4.0 – the future of welding
The future of professional welding is networked, digital and paperless. These are the challenges of “Industry 4.0” and every company must face these sooner or later.
The fourth Industrial Revolution has begun
The fourth industrial revolution is in full swing: many companies are facing the challenge of equipping their operations for the future with an intelligent man-machine network that increases productivity.
Since the 1970s, when the third Industrial Revolution began, routine procedures at industrial companies have been increasingly influenced by IT structures and automation. CNC machines, robots, and microprocessor-controlled welding machines have improved production processes and consequently also the quality of manufactured products. The resulting analysis of all process data, in real time, become possible by using industry 4.0 technology, makes unused potential visible and provides a decisive advantage on the global market.
The EWM group delivers welding companies the ideal solution with the new Titan XQ multiprocess MIG/MAG welding machine and the Welding 4.0 welding management system ewm Xnet 2.0.
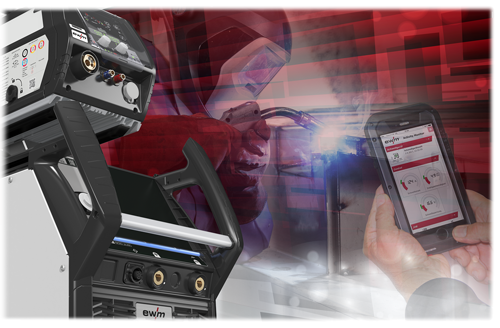
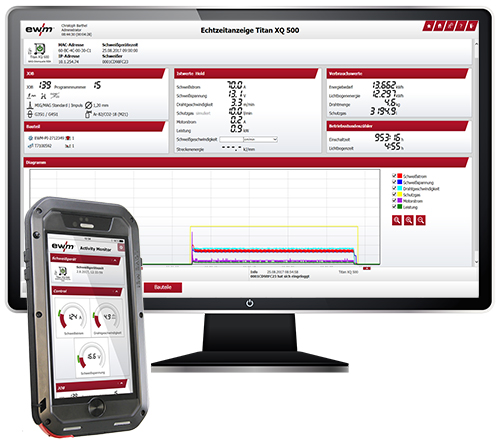
We are driving forward digitisation and development of welding technology
This is how we secure competitive advantages for our customers and accompany them along the path to becoming a pioneering Industry 4.0 company. The new generation of machines meets the expectations placed on modern machines in the 4.0 age. Intuitive, self-explanatory controls are the interface between man and machine.
Time is money – Real-time analysis of processes is invaluable
The digitalisation of machines thanks to highly intelligent microprocessors, memory interfaces and network connection facilities provides all the prerequisites which are needed for capturing process data, machine efficiency analyses and preventive maintenance.
The EWM group delivers welding companies the ideal solution with the new Titan XQ multiprocess MIG/MAG welding machine and the Welding 4.0 welding management system ewm Xnet 2.0 first-class future-proofability, for even more efficient, qualitative-certifiable welding.
ewm Xnet 2.0 welding management system
A step towards more efficient welding technology that saves resources
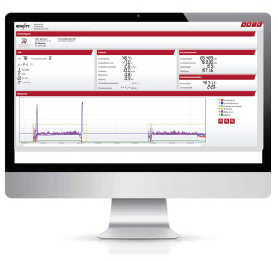
- Recording of welding data
- Save, review and analyse at a central point
- Online monitoring – control and monitor the welding process for any number of welding machines
- Analysis, evaluation, reporting and documentation of welding parameters recorded online
- Option of transferring to all welding machines in the network
- Convenient, easy-to-create graphical layout of all network participants
Xnet modules and components
- Starter set
Record and manage welding data and transmit consumption values in real time
- WPQ-X Manager
Create, manage and assign welding procedure specifications to welders yourself
- Xnet 2.0 component management
Manage components, create welding sequence plans, assign WPS
- Xbutton
Access authorisation and WPS assignment for welders via the robust hardware key
ewm Xnet 2.0 component management (module 3)
Step 1 –
Work preparation in ewm Xnet 2.0
- Create the component to be produced in ewm Xnet 2.0 during work preparation on PC in the office
- Create the component to be produced in the office on PC
- Create drawing file or import from CAD
- Determine seam sequence plan
- Assign WPS
- Print barcode, add the work order or attach directly to the component as a sticker
- Send component data to welding machine via LAN/WiFi
- The data is available offline in the machine e.g. for use on construction sites
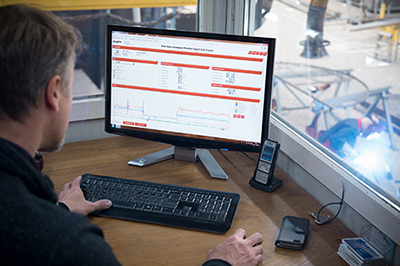
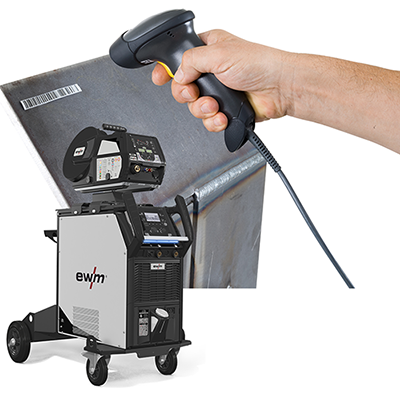
Step 2 -
Scan the barcode on the component
- Welder scans the barcode on the component using a barcode scanner
- Component data is called up on the control:
- Order numbers
- Component numbers
- Component group
- Series numbers
- Batch numbers
- Welding sequence plan (e.g. seam 1, run 1, seam 1, run 2 etc.)
- WPS (welding data for every run/seam)
- Required welding qualification
Step 3 -
Xbutton
- Welder identifies themselves for welding approval using the Xbutton on the welding machine
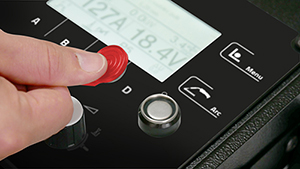
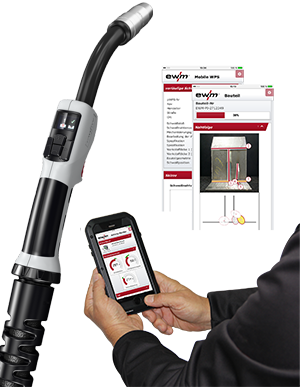
Step 4 -
Call up the beads and seams corresponding to the welding sequence plan using the PM welding torch and graphic display
- Welder begins working in line with the displayed seam sequence
- All welding parameters are set automatically for every individual run/seam by the machine
- After each run/seam, the welder confirms its completion by pressing a button on the PM welding torch with graphic display
- Two-part exit e.g. for tack-welding tasks using a button on the PM welding torch with graphic display
- Display with seams/runs